Why do explosion-proof cameras need anti-corrosion coatings?
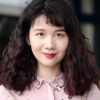
Huan He
Aug 2, 2024
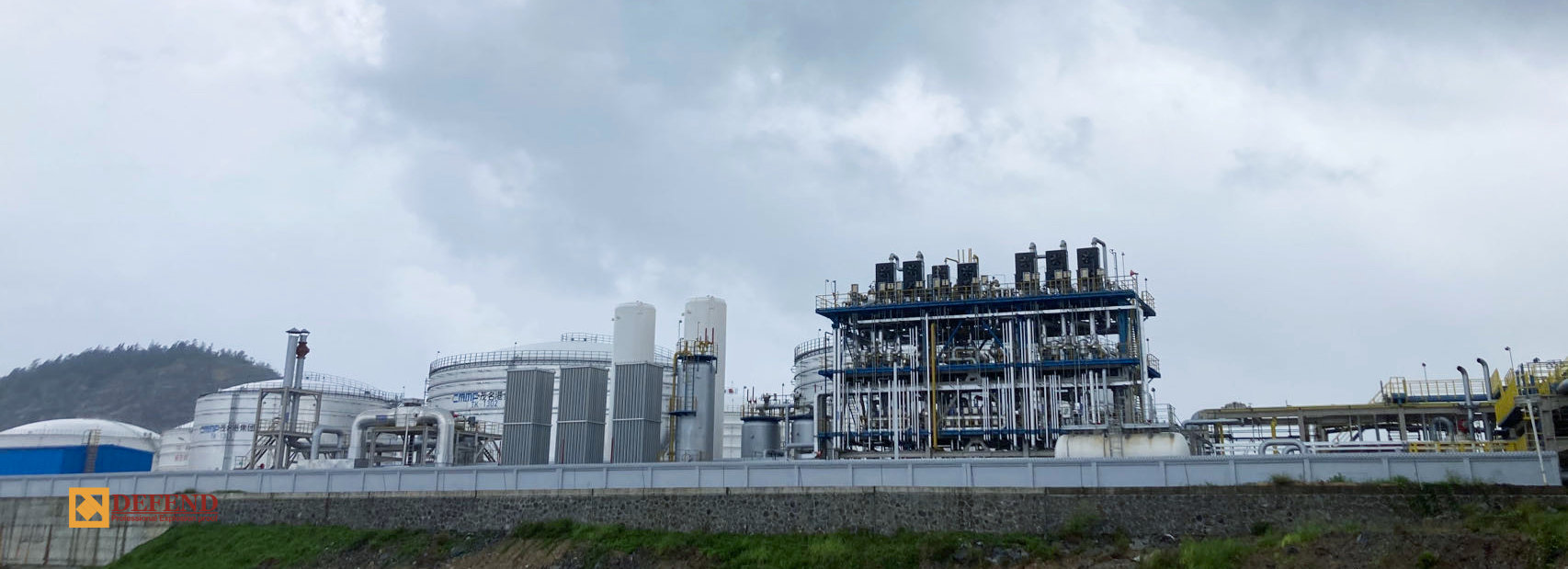
Explosion proof cameras need anti-corrosion coatings to ensure their longevity, reliability, and safety in harsh environments. Here are the key reasons:
Corrosive environments can cause the camera housing to deteriorate quickly. Anti-corrosion coatings protect the camera from rust and other forms of corrosion, extending its operational lifespan.
Explosion-proof cameras are designed to contain any sparks or explosions that might occur within the camera housing. Corrosion can weaken the structural integrity of the camera, compromising its ability to contain explosions and making it unsafe for use in hazardous areas.
Corrosion can damage the internal components of the camera, leading to malfunctions and reduced performance. Anti-corrosion coatings help maintain the camera's functionality by protecting its internal electronics from corrosive damage.
In industries where explosion-proof cameras are used, such as oil and gas, chemical plants, and marine environments, reliable monitoring is critical for safety and operational efficiency. Anti-corrosion coatings help ensure that the cameras remain functional and provide continuous monitoring without frequent breakdowns.
Corrosion can lead to frequent repairs and replacements, increasing maintenance costs. Anti-corrosion coatings help reduce these costs by minimizing the wear and tear on the cameras, leading to fewer maintenance requirements.
Many industries have strict regulations regarding the safety and maintenance of equipment used in hazardous environments. Anti-corrosion coatings help ensure that explosion-proof cameras meet these regulatory requirements by maintaining their safety standards.
By protecting explosion-proof cameras from corrosion, these coatings help ensure that the cameras can withstand the harsh conditions of their operating environments while maintaining safety and functionality.
Explosion-proof cameras need an anti-corrosion coating in environments where they are exposed to corrosive substances. Here are some scenarios where this is necessary:
-
Chemical Plants
These environments often have airborne chemicals and vapors that can corrode camera housings.
-
Offshore Oil and Gas Platforms
The salty sea air and the presence of hydrocarbons can be highly corrosive.
-
Marine Environments
Ports, ships, and coastal facilities have high salt concentrations in the air and water, which can cause corrosion.
-
Food and Beverage Industry
Certain food processing plants use cleaning agents and chemicals that can be corrosive.
-
Mining Operations
The presence of minerals and chemicals can lead to a highly corrosive environment.
-
Wastewater Treatment Plants
These facilities handle various corrosive substances that can damage equipment over time.
-
Fertilizer Plants
The production and handling of fertilizers often involve corrosive chemicals.